3D Bioprinting
Science in Space: December 2023 Imagine someone needs a heart transplant and scientists take cells from that person to create an entire new heart for them. Research on the International Space Station is helping to bring that dream closer to reality. The process of 3D printing (also known as additive manufacturing) enables the design and […]

Science in Space: December 2023
Imagine someone needs a heart transplant and scientists take cells from that person to create an entire new heart for them. Research on the International Space Station is helping to bring that dream closer to reality.
The process of 3D printing (also known as additive manufacturing) enables the design and production of one-of-a-kind items made of plastic, metal, and other materials, including tools, equipment, and even buildings. Biological printing or bioprinting uses living cells, proteins, and nutrients as raw materials and has the potential to produce human tissues for treating injury and disease and to create entire organs for transplants.
In Earth’s gravity, bioprinting requires a scaffold or other type of structure to support tissues, but in the near-weightlessness of the space station’s orbit, tissues grow in three dimensions without such support. Redwire Corporation developed the BioFabrication Facility (BFF) as a part of the larger goal of using microgravity to bioprint human organs. Popular Science magazine recently awarded the BFF a 2023 Best of What’s New Award in the Health Category. These awards, handed out since 1988, recognize “groundbreaking innovations changing our world,” according to Popular Science, and “radical ideas that are improving our everyday lives and our futures.”

A current investigation, BFF-Cardiac, uses the BFF to evaluate the printing and processing of cardiac tissue samples. Cardiovascular disease is the number one cause of death in the United States. Adult heart tissue is unable to regenerate, so damaged heart tissue is mostly replaced with scar tissue, which can block electrical signals and prevent proper cardiac contractions. This investigation could support the development of patches to replace damaged tissue – and eventually the creation of replacement hearts. The work represents a big step toward addressing the significant gap between the number of transplant organs needed and available donors.
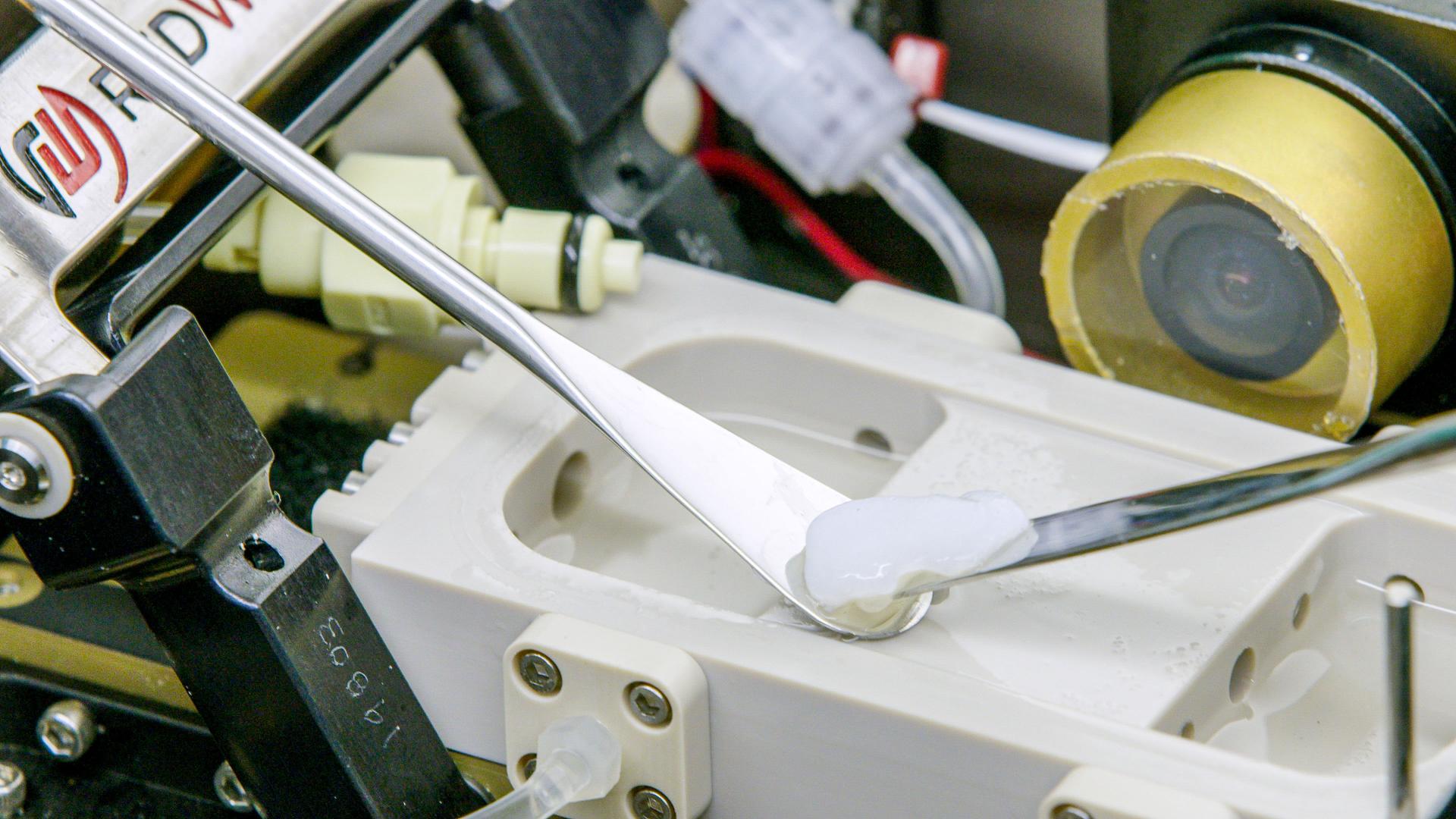
The BFF-Meniscus investigation and the follow-up BFF-Meniscus-2 investigation resulted in the first successful bioprinting of a human knee meniscus in orbit using the space station’s BioFabrication Facility, announced in September 2023. Musculoskeletal injuries, including tears in the meniscus, are one of the most common injuries for the U.S. military and this milestone is a step toward developing improved treatments on the ground and for crew members who experience musculoskeletal injuries on future space missions. After initial printing and a period of growth in microgravity, the tissues returned to Earth for additional analysis and testing.
The Russian state space agency ROSCOSMOS launched equipment in 2018, 3D MBP, that included a magnetic printer called Organ.Aut. A series of experiments from 2018 through 2020 showed that this approach could create tissue constructs, helping to pave the way for additional research on producing artificial organs.
Bioprinting technology also could create artificial retinas to help restore sight for the 30 million people worldwide who suffer from degenerative retinal diseases. One way to manufacture artificial retinas is a technique that alternates layers of a light-activated protein and a binder on a film. On Earth, gravity affects the quality of these films, but researchers suspected that films created in microgravity would be more stable and have higher optical clarity. Protein-Based Artificial Retina Manufacturing is one of several investigations by LambdaVision Inc. in partnership with developer Space Tango Inc. to develop and validate space-based manufacturing methods for artificial retinas. The company has consistently manufactured multiple 200-layer artificial retina films in microgravity and now is working to commercialize its hardware and strategies for development of other therapies and drugs.
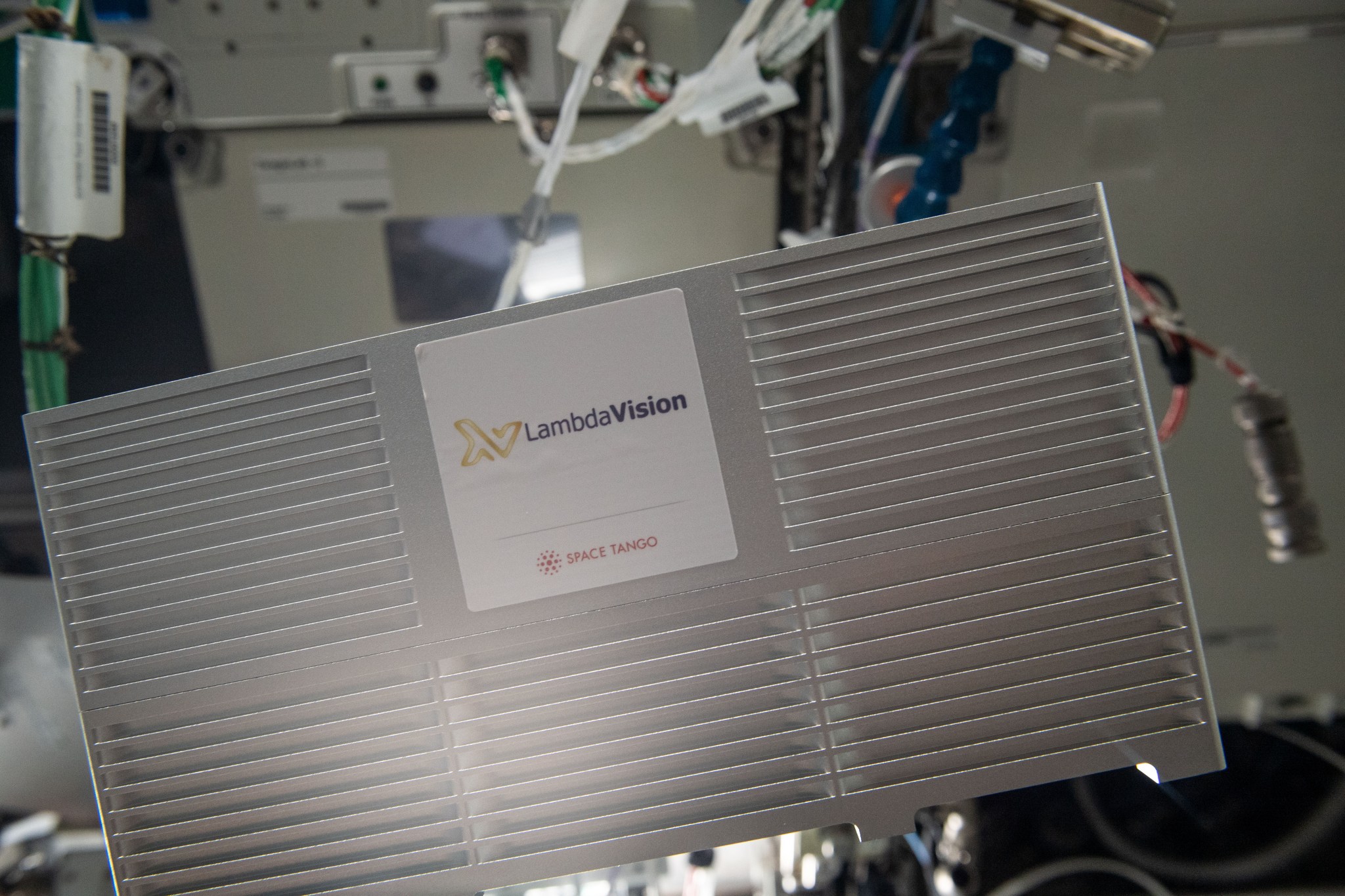
Bioprint FirstAid, a study from ESA (European Space Agency) and the German Space Agency (DLR), demonstrated the function of a prototype for a portable handheld bioprinter that creates a patch from a patient’s own skin cells. Space causes changes in the wound healing process, and such customized bandages could accelerate healing on future missions to the Moon and Mars. Using cultured cells from the patient reduces the risk of rejection by the immune system, and the device offers greater flexibility to address wound size and position. Because the device is small and portable, health care workers could take it almost anywhere on Earth. The investigation showed that the device works as intended in microgravity, and researchers are studying the space-printed patches and comparing them with samples printed on the ground before taking the next step.
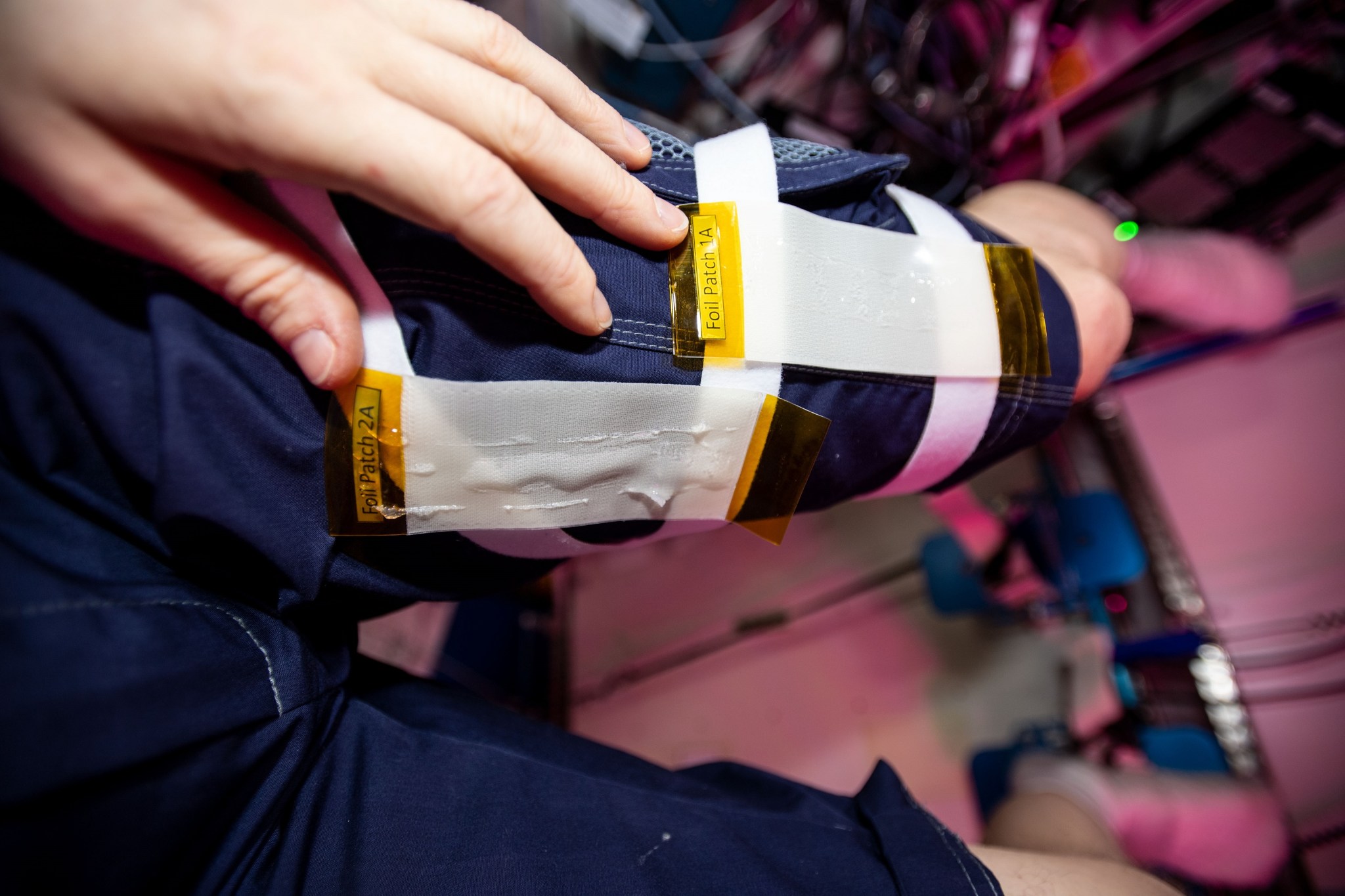
Bioprinting in microgravity also could make it possible to produce food and medicine on demand on future space missions. Such capabilities would reduce the mass and cost of materials needed at launch and help maintain the health and safety of crew members throughout a mission.
The 3D Printing In Zero-G investigation, which started in 2014, demonstrated that the process of 3D printing with inorganic materials such as plastic worked normally in microgravity.1 3D printing could reduce the need to pack costly spare parts on future long-term missions and help solve the problem of trying to predict every tool or object that might be needed on a mission. With the addition of bioprinting capabilities, crews eventually may be able to 3D print almost anything they need – from a replacement screwdriver to a replacement knee.
John Love, ISS Research Planning Integration Scientist
Expedition 70
Search this database of scientific experiments to learn more about those mentioned above.
Citations:
1 Prater TJ, Bean QA, Werkheiser N, Grguel R, Beshears RD, Rolin TD, Huff T, Ryan RM, Ledbetter III FE, Ordonez EA. Analysis of specimens from phase I of the 3D Printing in Zero G Technology demonstration mission. Rapid Prototyping Journal. 2017 October 6; 23(6): 1212-1225. DOI: 10.1108/RPJ-09-2016-0142.
What's Your Reaction?
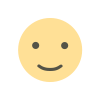
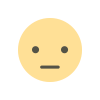
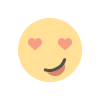
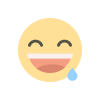
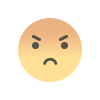
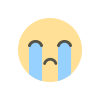
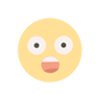