Science Launches to Space Station on NASA’s 20th Northrop Grumman Mission
Tests of a 3D metal printer, semiconductor manufacturing, and thermal protection systems for reentry to Earth’s atmosphere are among the scientific investigation that NASA and international partners are launching to the International Space Station on Northrop Grumman’s 20th commercial resupply services mission. The company’s Cygnus cargo spacecraft is scheduled to launch on a SpaceX Falcon […]
Science Launches to Space Station on NASA’s 20th Northrop Grumman Mission
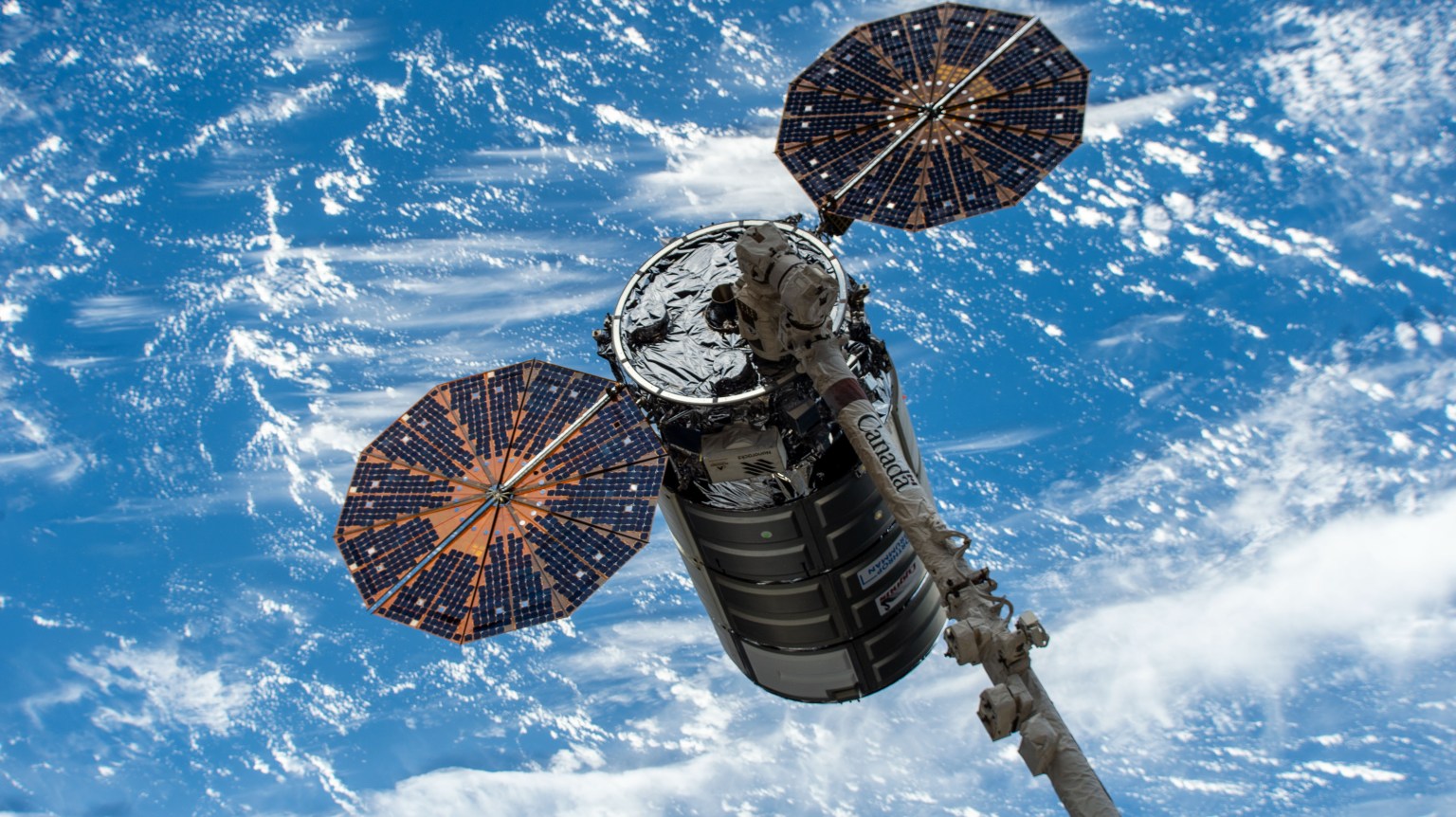
Tests of a 3D metal printer, semiconductor manufacturing, and thermal protection systems for reentry to Earth’s atmosphere are among the scientific investigation that NASA and international partners are launching to the International Space Station on Northrop Grumman’s 20th commercial resupply services mission. The company’s Cygnus cargo spacecraft is scheduled to launch on a SpaceX Falcon 9 rocket from Cape Canaveral Space Force Station in Florida by late January.
Read more about some of the research making the journey to the orbiting laboratory:
3D Printing in Space
An investigation from ESA (European Space Agency), Metal 3D Printer tests additive manufacturing or 3D printing of small metal parts in microgravity.
“This investigation provides us with an initial understanding of how such a printer behaves in space,” said Rob Postema of ESA. “A 3D printer can create many shapes, and we plan to print specimens, first to understand how printing in space may differ from printing on Earth and second to see what types of shapes we can print with this technology. In addition, this activity helps show how crew members can work safely and efficiently with printing metal parts in space.”
Results could improve understanding of the functionality, performance, and operations of metal 3D printing in space, as well as the quality, strength, and characteristics of the printed parts. Resupply presents a challenge for future long-duration human missions. Crew members could use 3D printing to create parts for maintenance of equipment on future long-duration spaceflight and on the Moon or Mars, reducing the need to pack spare parts or to predict every tool or object that might be needed, saving time and money at launch.
Advances in metal 3D printing technology also could benefit potential applications on Earth, including manufacturing engines for the automotive, aeronautical, and maritime industries and creating shelters after natural disasters.
A team led by Airbus U.S. Space & Defense and Space SAS under a contract with ESA developed the investigation.
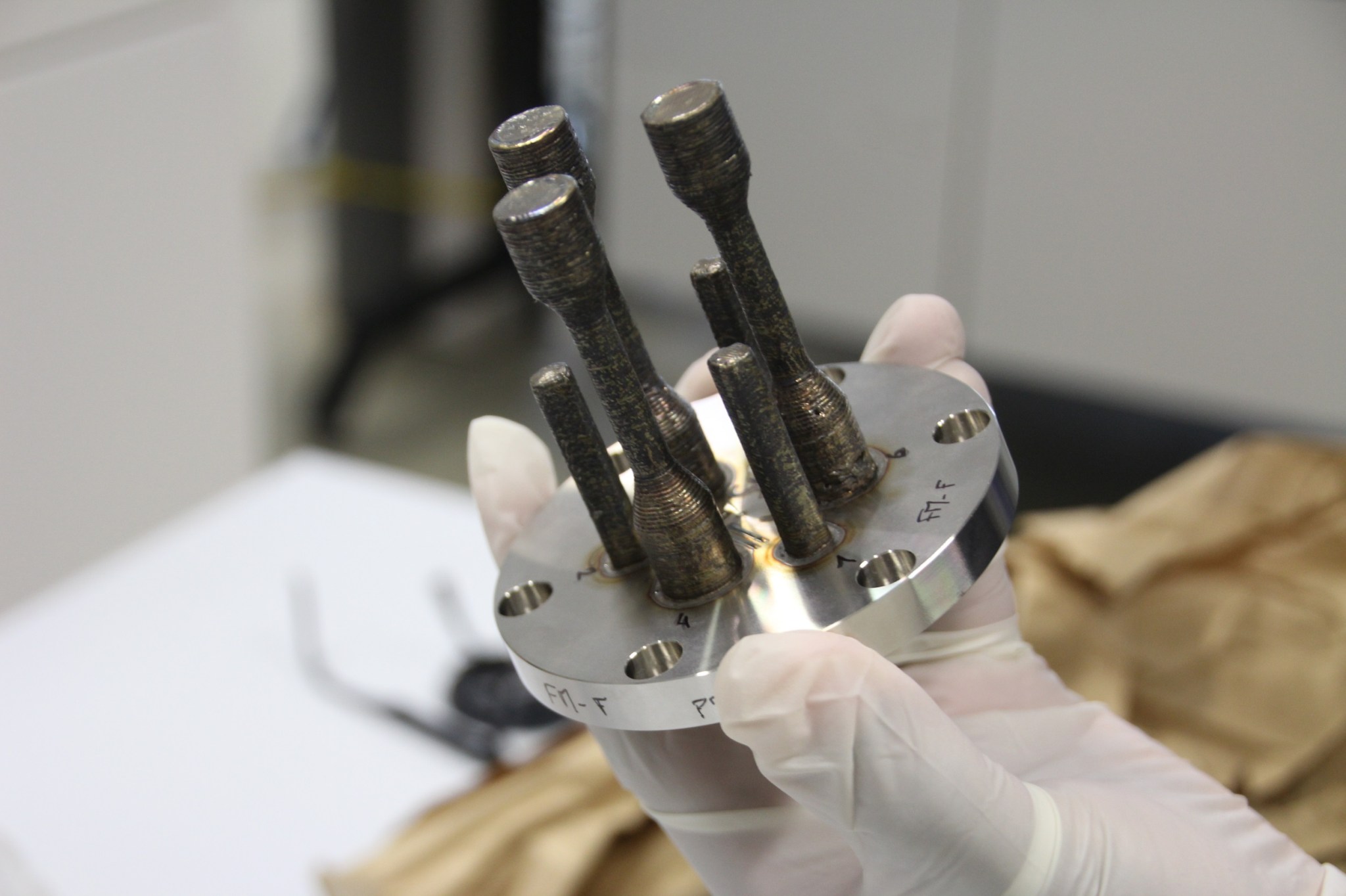
Semiconductor Manufacturing in Microgravity
Manufacturing of Semiconductors and Thin-Film Integrated Coatings (MSTIC) examines how microgravity affects thin films that have a wide range of uses.
“The potential for producing films with superior surface structures and the broad range of applications from energy harvesting to advanced sensor technology are particularly groundbreaking,” said Alex Hayes of Redwire Space, which developed the technology. “This represents a significant leap in space manufacturing and could herald a new era of technological advancements with wide-reaching implications for both space exploration and terrestrial applications.”
This technology could enable autonomous manufacturing to replace the many machines and processes currently used to make a wide range of semiconductors, potentially leading to the development of more efficient and higher-performing electrical devices.
Manufacturing semiconductor devices in microgravity also may improve their quality and reduce the materials, equipment, and labor required. On future long-duration missions, this technology could provide the capability to produce components and devices in space, reducing the need for resupply missions from Earth. The technology also has applications for devices that harvest energy and provide power on Earth.
“While this initial pilot program is designed to compare thin films produced on Earth and in space, the ultimate goal is to expand to producing a diverse range of production areas within the semiconductor field,” Hayes said.
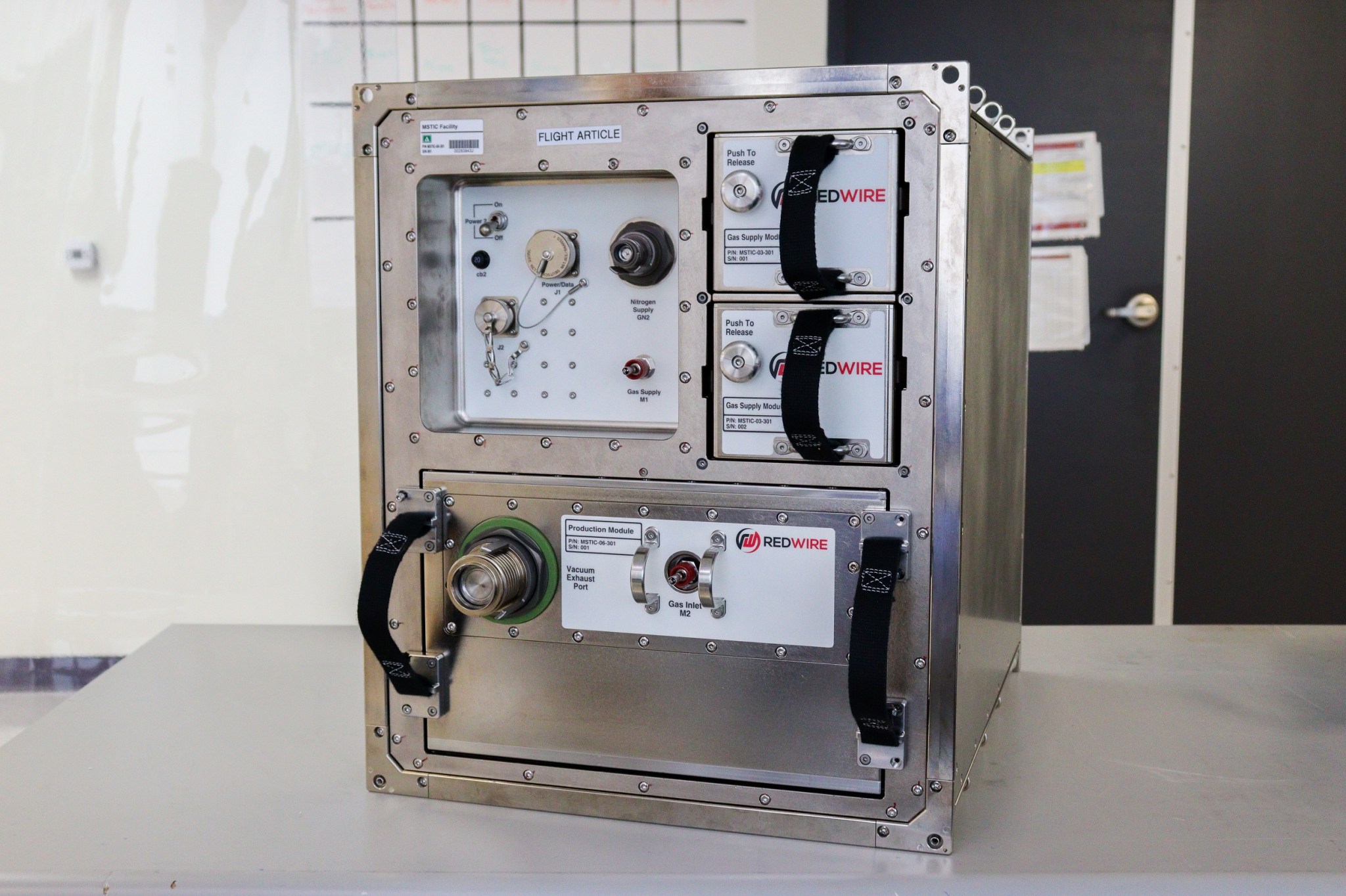
Modeling Atmospheric Re-entry
Scientists who conduct research on the space station often return their experiments to Earth for additional analysis and study. But the conditions that spacecraft experience during atmospheric reentry, including extreme heat, can have unintended effects on their contents. Thermal protection systems used to shield spacecraft and their contents are based on numerical models that often lack validation from actual flight, which can lead to significant overestimates in the size of system needed and take up valuable space and mass. Kentucky Re-entry Probe Experiment-2 (KREPE-2), part of an effort to improve thermal protection system technology, uses three capsules outfitted with different heat shield materials and a variety of sensors to obtain data on actual reentry conditions.
“Building on the success of KREPE-1, we have improved the sensors to gather more measurements and improved the communication system to transmit more data,” said principal investigator Alexandre Martin at the University of Kentucky. “We have the opportunity to test several heat shields provided by NASA that have never been tested before, and another manufactured entirely at the University of Kentucky, also a first.”
The capsules can be outfitted for other atmospheric re-entry experiments, supporting improvements in heat shielding for applications on Earth, such as protecting people and structures from wildfires.

Remote Robotic Surgery
Robotic Surgery Tech Demo tests the performance of a small robot that can be remotely controlled from Earth to perform surgical procedures. Researchers plan to compare procedures in microgravity and on Earth to evaluate the effects of microgravity and time delays between space and ground.
The robot uses two “hands” to grasp and cut simulated surgical tissue and provide tension that is used to determine where and how to cut, according to Shane Farritor, chief technology officer at Virtual Incision Corporation, developer of the investigation with the University of Nebraska.
Longer space missions increase the likelihood that crew members may need surgical procedures, whether simple stiches or an emergency appendectomy. Results from this investigation could support development of robotic systems to perform these procedures. In addition, the availability of a surgeon in rural areas of the country declined nearly a third between 2001 and 2019. Miniaturization and the ability to remotely control the robot may help to make surgery available anywhere and anytime.
NASA has sponsored research on miniature robots for more than 15 years. In 2006, remotely operated robots performed procedures in the underwater NASA’s Extreme Environment Mission Operations (NEEMO) 9 mission. In 2014, a miniature surgical robot performed simulated surgical tasks on the Zero-G parabolic airplane.
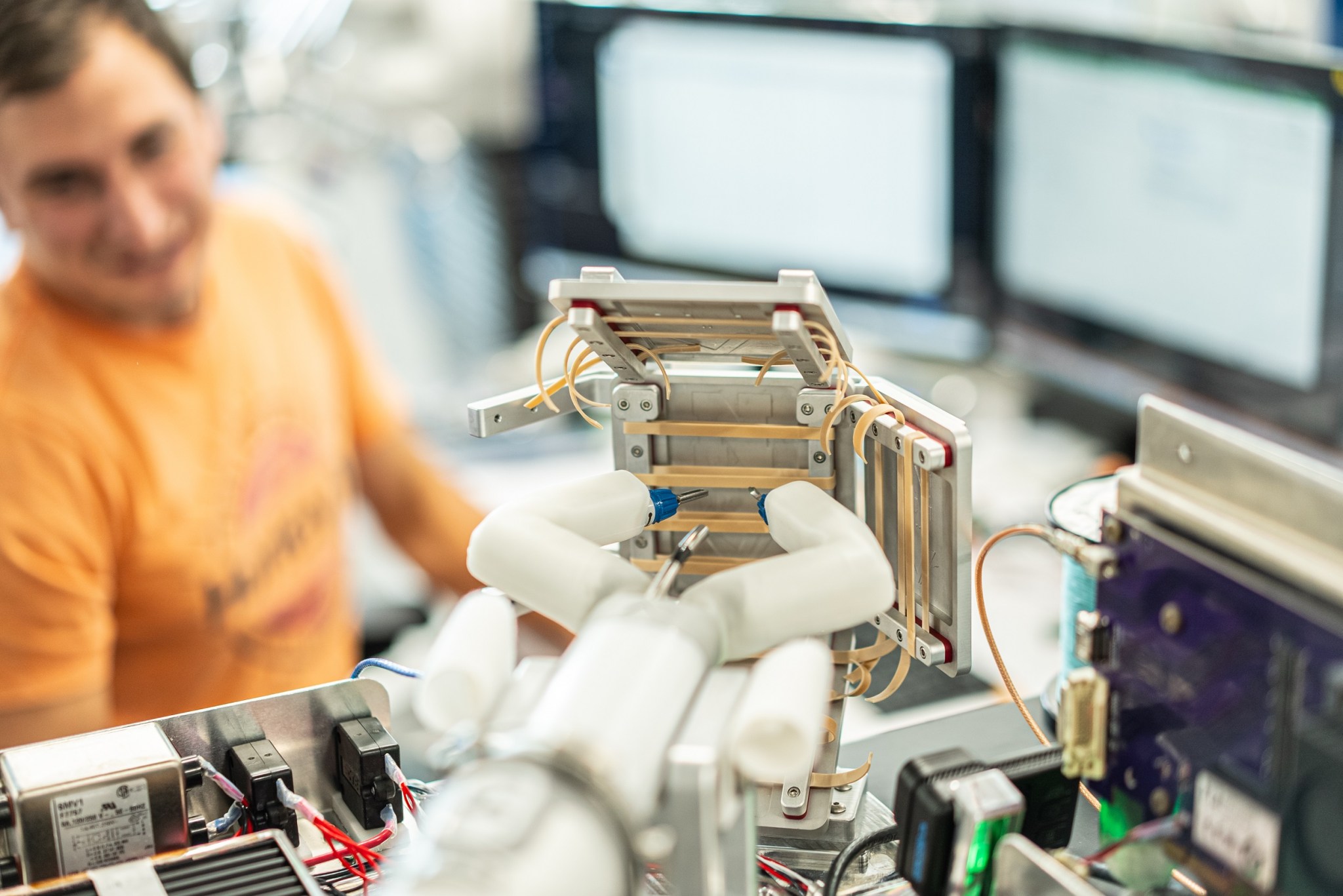
Growing Cartilage Tissue in Space
Compartment Cartilage Tissue Construct demonstrates two technologies, Janus Base Nano-Matrix (JBNm) and Janus Base Nanopiece (JBNp). JBNm is an injectable material that provides a scaffold for formation of cartilage in microgravity, which can serve as a model for studying cartilage diseases. JBNp delivers an RNA-based therapy to combat diseases that cause cartilage degeneration.
Cartilage has a limited ability to self-repair and osteoarthritis is a leading cause of disability in older patients on Earth. Microgravity can trigger cartilage degeneration that mimics the progression of aging-related osteoarthritis but happens more quickly, so research in microgravity could lead to faster development of effective therapies. Results from this investigation could advance cartilage regeneration as a treatment for joint damage and diseases on Earth and contribute to development of ways to maintain cartilage health on future missions to the Moon and Mars.
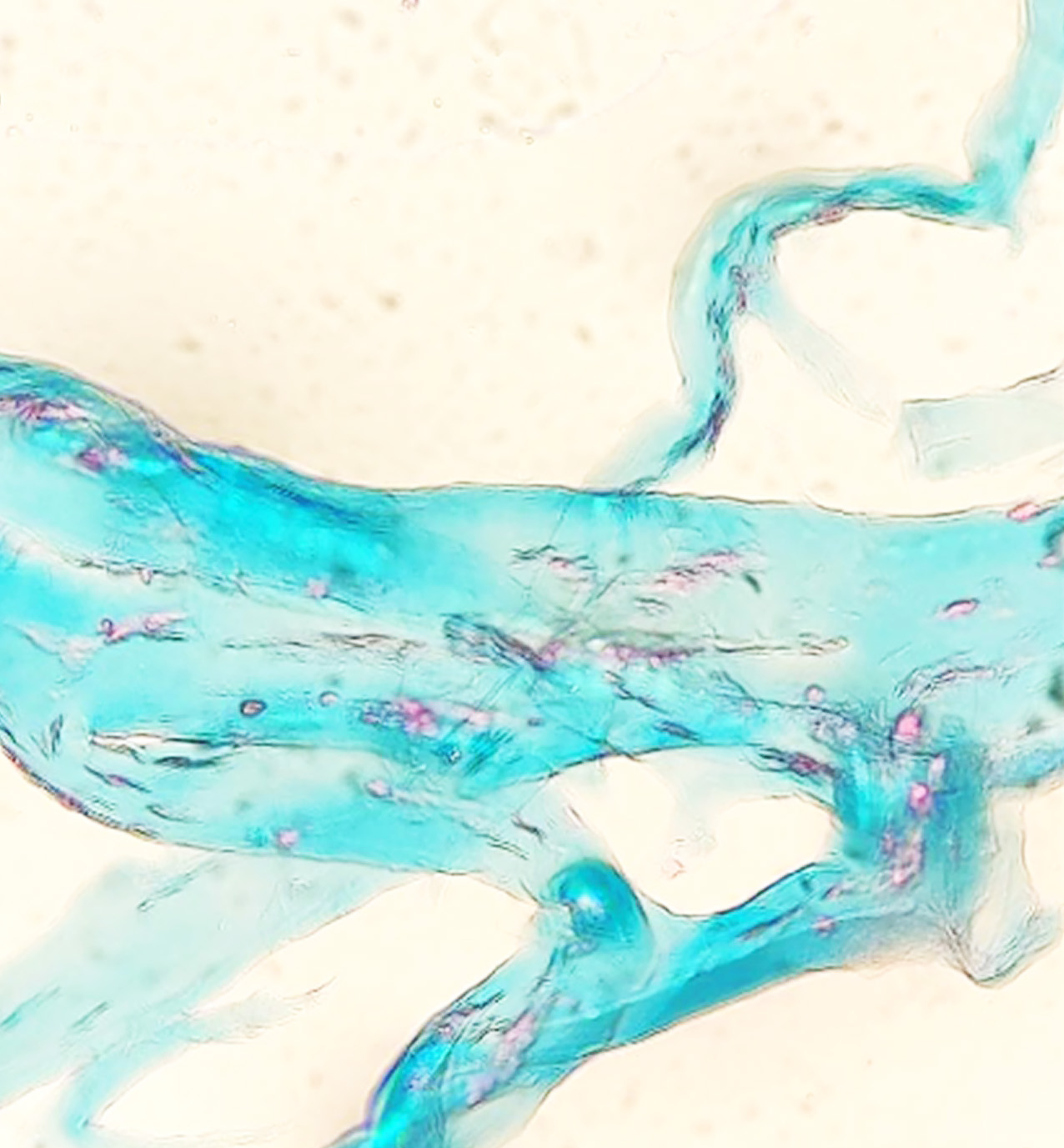
Melissa Gaskill
International Space Station Program Research Office
Johnson Space Center
Search this database of scientific experiments to learn more about those mentioned above.
What's Your Reaction?
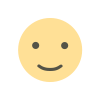
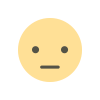
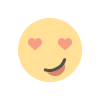
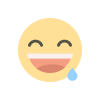
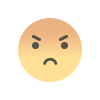
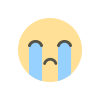
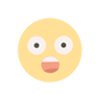