The Marshall Star for August 7, 2024
NASA Additive Manufacturing Project Shapes Future for Agency, Industry Rocket Makers The widespread commercial adoption of additive manufacturing technologies, commonly known as 3D printing, is no surprise to design engineers at NASA’s Marshall Space Flight Center whose research created stronger, lighter weight materials and new manufacturing processes to make rocket parts. NASA’s RAMPT (Rapid Analysis […]
The Marshall Star for August 7, 2024

NASA Additive Manufacturing Project Shapes Future for Agency, Industry Rocket Makers
The widespread commercial adoption of additive manufacturing technologies, commonly known as 3D printing, is no surprise to design engineers at NASA’s Marshall Space Flight Center whose research created stronger, lighter weight materials and new manufacturing processes to make rocket parts.
NASA’s RAMPT (Rapid Analysis and Manufacturing Propulsion Technology) project is on the cutting edge of additive manufacturing – helping the agency and industry produce new alloys and additively manufactured parts, commonly referred to as 3D printing, according to Paul Gradl, the project’s co-principal investigator at Marshall.
“Across NASA’s storied legacy of vehicle and hardware design, testing, and integration, our underlying strength is in our application of extremely durable and severe environment materials and innovative manufacturing for component design,” said Gradl. “We strive to fully understand the microstructure and properties of every material and how they will ultimately be used in components before we make them available to industry for flight applications.”
The same principle applies to additive manufacturing, the meticulous process of building components and hardware one layer of material at a time.
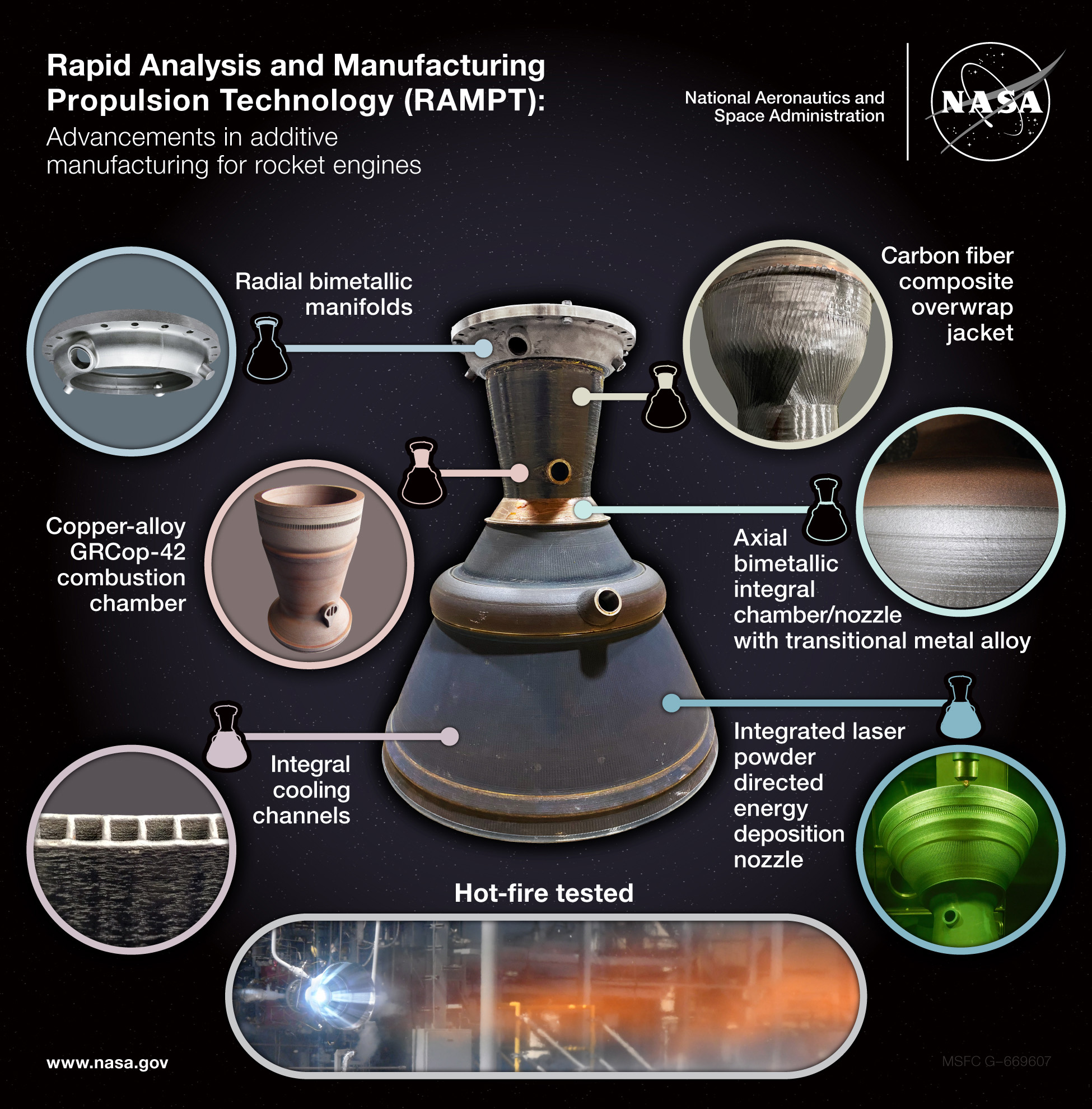
“The RAMPT project’s goal is to support commercial, technical readiness, enabling our industry partners to meet the challenges inherent in building new generations of safer, more cost-effective deep space exploration propulsion systems,” said John Fikes, RAMPT project manager.
Since its inception, RAMPT has conducted 500 test-firings of 3D-printed injectors, nozzles, and chamber hardware totaling more than 16,000 seconds, using newly developed extreme-environment alloys, large-scale additive manufacturing processes, and advanced composite technology. The project has also started developing a full-scale version for the workhorse RS-25 engine – which experts say could reduce its costs by up to 70% and cut manufacturing time in half.
As printed structures are getting bigger and more complex, a major area of interest is the additive manufacturing print scale. A decade ago, most 3D-printed parts were no bigger than a shoebox. Today, additive manufacturing researchers are helping the industry produce lighter, more robust, intricately designed rocket engine components 10-feet tall and eight-feet in diameter.
“NASA, through public-private partnerships, is making these breakthroughs accessible to the commercial space industry to help them rapidly advance new flight technologies of their own,” Gradl said. “We’re solving technical challenges, creating new supply chains for parts and materials, and increasing the industry’s capacity to rapidly deliver reliable hardware that draws a busy commercial space infrastructure ever closer.”
The RAMPT project does not just develop the end technology but the means to fully understand that technology, whatever the application. That means advancing cutting-edge simulation tools that can identify the viability of new alloys and composites at the microstructural level – assessing how they handle the fiery rigors of liftoff, the punishing cold of space, and the dynamic stresses associated with liftoffs, landings, and the long transits between.
NASA’s strategy to encourage commercial and academic buy-in is to offer public-private partnership opportunities, wherein industry and academia contribute as much as 25% of project development costs, allowing them to reap the benefits.
For example, NASA successfully delivered a refined version of an alloy, known as GRCop42, created at NASA’s Glenn Research Center nearly 40 years ago which helped commercial launch provider, Relativity Space, launch the first fully 3D-printed rocket in March 2023.
“Our primary goal with these higher-performance alloys is to prove them in a rocket engine test-fire environment and then hand them off to enable commercial providers to build hardware, fly launch vehicles, and foster a thriving space infrastructure with real scientific, social, and economic rewards,” Gradl said.
A key benefit of additive manufacturing hardware development is radically reducing the “design-fail-fix” cycle – when engineers develop new hardware, ground-test it to failure to determine the hardware’s design limits under all possible conditions and then tweak accordingly. That capability is increasingly important with the creation of new alloys and designs, new processing techniques, and the introduction of composite overwraps and other innovations.
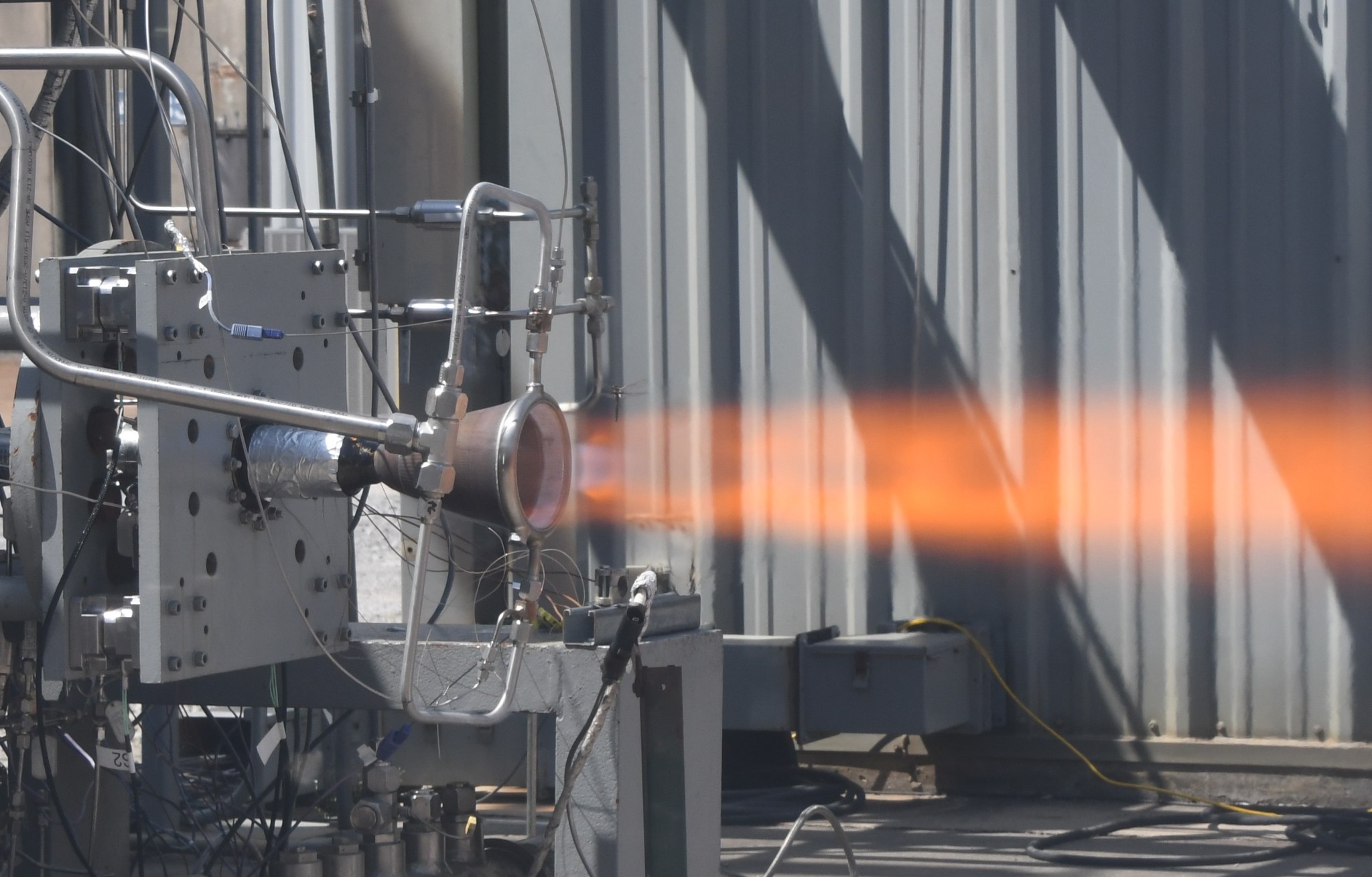
The RAMPT project did just that, successfully advancing new additive manufacturing alloys and processes, integrating them with carbon-fiber composites to reduce weight by up to 40%, developing and validating new simulation tools – and making all this data available to industry through public-private partnerships.
“We’re able to deliver prototypes in weeks instead of years, conduct dozens of scaled ground tests in a period that would feasibly permit just one or two such tests of conventionally manufactured hardware, and most importantly, deliver technology solutions that are safer, lighter, and less costly than traditional components,” Gradl said.
Fikes added, “Ten years from now, we may be building rocket engines – or rockets themselves – out of entirely new materials, employing all-new processing and fabrication techniques. NASA is central to all of that.”
The RAMPT project continues to progress and receive recognition from NASA and industry partners. On July 31, the RAMPT team was awarded NASA’s 2024 Invention of The Year award for its excellence and contributions to NASA and the commercial industry’s deep space exploration goals.
Marshall leads RAMPT, with key support among engineers and technologists at NASA’s Glenn Research Center; Ames Research Center; Langley Research Center; and Auburn University in Auburn, Alabama, plus contributions from other academic partners and industry contractors. RAMPT is funded by NASA’s Game Changing Development Program within the agency’s Space Technology Mission Directorate.
Artemis Mission Manager Mike Sarafin Speaker for Aug. 8 Mission Success Forum
By Wayne Smith
Mike Sarafin, Artemis mission manager and Mission Management Team chair, will be the guest speaker for the Mission Success is in Our Hands Shared Experiences Forum on Aug. 8 at NASA’s Marshall Space Flight Center.
The 11:30 a.m. event will be in Activities Building 4316 and Marshall team members are encouraged to attend. The forum is available to NASA employees and the public virtually via Teams.
Mission Success is in Our Hands is a safety initiative collaboration between NASA’s Marshall Space Flight Center and Jacobs Engineering. The initiative’s goal to help team members make meaningful connections between their jobs and the safety and success of NASA and Marshall missions.
The theme of the forum is “Artemis I Mission Challenges.” Sarafin will provide a frontline perspective on the role of the Mission Management Team and how it is governed. He will summarize key challenges encountered, suggest best practices for managing large diverse teams, discuss useful risk informed decision-making tools, and highlight lessons learned for consideration in future human lunar exploration missions.
“As we continue to prepare for the next Artemis mission, this forum is a valuable opportunity to learn about challenges NASA faced to ensure mission success for Artemis I,” said Bill Hill, director of the Safety and Mission Assurance Directorate at Marshall. “I encourage Marshall team members to attend the forum in person to gain Mike’s insight on safety and mission success.”
Sarafin is the Artemis mission manager for the Moon to Mars Program Office at NASA Headquarters. In this role, he leads the Mission Management Team for Artemis, providing oversight and responsibility for critical decisions across all flight phases (launch, in-space, and recovery), with support from team members and advisors with technical expertise in various areas. Prior to flight, he acted as a senior technical leader integrating mission requirements, planning, operations, and flight readiness leading to mission execution.
With more than 30 years of human spaceflight experience, Sarafin began his career as a guidance, navigation, and mission controller working on the space shuttle. He became a NASA flight director supporting the space shuttle and the International Space Station. He also was the lead flight director for Orion’s first flight test in 2014.
As part of the forum, Mission Success is in Our Hands will present the Golden Eagle Award to a Marshall team member. The award promotes awareness and appreciation for flight safety, as demonstrated through the connections between employees’ everyday work, the success of NASA and Marshall’s missions, and the safety of NASA astronauts. The award recognizes individuals who have made significant contributions to flight safety and mission assurance above and beyond their normal work requirements. Management or peers can nominate any team member for the award. Honorees are typically recognized at quarterly Shared Experiences forums.
The next Shared Experiences Forum is scheduled for Sept. 5, featuring Dave Dykhoff, former vice president and general manager of the Jacobs Missile Defense Group and the NORAD Operations Group.
Smith, a Media Fusion employee and the Marshall Star editor, supports the Marshall Office of Communications.
Denise Smithers Named Marshall’s Center Executive Officer
Denise Smithers has been named to the position of center executive officer as part of a six-month detail supporting the Office of the Center Director at NASA’s Marshall Space Flight Center, effective Aug. 9. As center executive officer, Smithers will lead the overall office management and operations within the director’s office, integrate and coordinate center-wide actions, and serve as Marshall’s chief of staff.
Smithers has been with Marshall for more than 30 years, holding various budget, strategic, and leadership positions. Since July 2020, Smithers has served as a supervisory budget analyst for the Mission Support Office, overseeing a team of analysts in managing budgets for institutional support offices. While working in the Budget, Integration, and Analysis Team in the Office of the Chief Financial Officer (OCFO), she developed strategic guidance, managed processes, and provided in-depth analyses for the annual Planning, Programming, Budget, and Execution process. She was also responsible for reporting on financial performances, assessing trends, addressing cost-cutting issues, identifying risks, and providing strategic budgetary decisions.
Before joining OCFO, Smither’s previous roles included deputy director of the Office of Diversity and Equal Opportunity (ODEO) from 2019-2020, where she promoted education, awareness, and communication of diversity initiatives to Marshall’s workforce; lead budget analyst supporting the Chief Information Office from 2014-2019; external relations specialist from 2013-2014; technical assistant supporting the Office of the Center Director from 2011-2013; budget analyst from 2000-2013; and contract specialist from 1996-2000.
Smithers started her tenure at Marshall at 18 as a summer intern. In addition to her job duties, she is active in many community civic organizations and Employee Resource Groups (ERGs) at Marshall. She leads the OCFO Enterprise Diversity Equity Inclusion and Accessibility (DEIA) Culture, Branding, and Vision Team, and represents management on their focus team. She was appointed to the Marshall Culture Advisory Committee where she develops, implements, and accesses DEIA strategies and initiatives in collaboration with ODEO. Smithers also leads the Women’s ERG at Marshall and serves as the Blueprint to Reinforce Inclusivity and Diversity to Gain Equity (BRIDGE) Champion representative for OCFO.
A native of Athens, Alabama, Smithers earned a Master of Business Administration from Alabama A&M University and a Bachelor of Science degree from the University of Alabama in Huntsville. She was awarded a Silver Snoopy in 2011, a Director’s Commendation in 2019, and the Agency DEIA Medal in 2023.
Shooting Stars: Annual Perseid Meteor Shower to Peak Aug. 11-12
By Wayne Smith
They may not attract as much attention as last month’s daylight fireball over New York City, but stargazers can still anticipate seeing some shooting stars with the upcoming Perseid meteor shower. Caused by Earth passing through trails of debris left behind by Comet Swift-Tuttle, the shower has become famous over the centuries because of its consistent display of celestial fireworks.
“The Perseids is the best annual meteor shower for the casual stargazer,” said Bill Cooke, who leads NASA’s Meteoroid Environment Office at the agency’s Marshall Space Flight Center. “Not only is the shower rich in bright meteors and fireballs – No. 1 in fact – it also peaks in mid-August when the weather is still warm and comfortable. This year, the Perseid maximum will occur on the night of Aug. 11 and pre-dawn hours of Aug. 12. You’ll start seeing meteors from the shower around 11 p.m. local time and the rates will increase until dawn. If you miss the night of the 11th, you will also be able to see quite a few on the night of the 12th between those times.”
The best way to see the Perseids is to find the darkest possible sky and visit between midnight and dawn on the morning of Aug. 12. Allow about 45 minutes for your eyes to adjust to the dark. Lie on your back and look straight up. Avoid looking at cell phones or tablets because their bright screens ruin night vision and take your eyes off the sky.
Perseid meteors travel at the blistering speed of 132,000 mph – or 500 times faster than the fastest car in the world. At that speed, even a smidgen of dust makes a vivid streak of light when it collides with Earth’s atmosphere. Peak temperatures can exceed 3,000 degrees Fahrenheit as they speed across the sky. The Perseids pose no danger to people on the ground as practically all burn up 60 miles above our planet.
The first Perseid captured by NASA’s All Sky Meteor Camera Network was recorded at 9:48 p.m. EDT on July 23. The meteor – about as bright as the planet Jupiter, so not quite bright enough to be considered a fireball – was caused by a piece of Comet Swift-Tuttle about 5 millimeters in diameter entering the atmosphere over the Atlantic and burning up 66 miles above St. Cloud, Florida, just south of Orlando.
Rare Fireball in New York, New York Not Perseids
It wasn’t part of the Perseids, but a rare daylight fireball streaked across the sky over New York City at 11:15 a.m. EDT on July 16. The event gained national attention and was reported in media outlets across the U.S.
The fireball, defined as a meteor brighter than the planet Venus, is estimated to have soared over New York City before traversing a short path southwest and disintegrating about 31 miles above Mountainside, New Jersey. Cooke said the meteor was likely about 1 foot in diameter, which would have made the rock bright enough to see during the day. Seeing a meteor of this size is rarer than catching sight of the smaller particles a few millimeters in size typically seen in the night sky.
“To see one in the daytime over a populated area like New York is fairly rare,” Cooke said during an interview with ABC 7 in New York.
The Meteoroid Environments Office studies meteoroids in space so that NASA can protect our nation’s satellites, spacecraft and even astronauts aboard the International Space Station from these bits of tiny space debris.
For more skywatching highlights in April, check out Jet Propulsion Lab’s What’s Up series.
Smith, a Media Fusion employee and the Marshall Star editor, supports the Marshall Office of Communications.
NASA Invites Public to Attend Deep Space Food Challenge Finale
NASA invites the public to explore the nexus of space and food innovation at the agency’s Deep Space Food Challenge symposium and winners’ announcement at the Nationwide and Ohio Farm Bureau 4-H Center in Columbus, Ohio, on Aug. 16.
In 2019, NASA and the CSA (Canadian Space Agency) started the Deep Space Food Challenge, a multi-year international effort to develop sustainable food systems for long-duration habitation in space including the Moon and Mars. Since Phase 1 of the challenge opened in 2021, more than 300 teams from 32 countries have developed innovative food system designs. On Aug. 16, NASA will announce the final Phase 3 winners and recognize the shared global effort.
NASA will award up to $1.5 million during the awards ceremony, totaling the prize purse for this three-year competition at $3 million. International teams also will be recognized for their achievements.
“Advanced food systems also benefit life on Earth,” said Kim Krome-Sieja, acting program manager of NASA Centennial Challenges at NASA’s Marshall Space Flight Center. “Solutions from this challenge could enable new avenues for food production around the world, especially in extreme environments, resource-scarce regions, and in locations where disasters disrupt critical infrastructure.”
The Methuselah Foundation, NASA’s partner in the Deep Space Food Challenge, is hosting the event in coordination with the Ohio State University College of Food, Agricultural, and Environmental Sciences and NASA Centennial Challenges.
“Our Phase 2 winners’ event in Brooklyn, New York, was an incredible display of innovation, partnership, and collaboration across NASA, industry, and academia,” said Angela Herblet, challenge manager of the Deep Space Food Challenge and program analyst of NASA Centennial Challenges at Marshall. “I’m looking forward to celebrating these brilliant Phase 3 finalists and underscoring the giant leaps they’ve made toward creating sustainable, regenerative food production systems.”
The event will feature a meet and greet with the Phase 3 finalists, symposium panels, and live demonstrations of the finalists’ food production technologies. Attendees also will have the opportunity to meet the crew of Ohio State students called “Simunauts,” who managed operations of the technologies during the eight-week demonstration and testing period.
“The Prizes, Challenges, and Crowdsourcing team is excited to welcome media, stakeholders, and the public to our event in Columbus,” said Amy Kaminski, program executive for NASA’s Prizes, Challenges, and Crowdsourcing at NASA Headquarters. “These finalists have worked diligently for three years to develop their diverse, innovative food systems, and I’m excited to see how their technologies may impact NASA’s future deep space missions.”
The awards ceremony also will livestream on Marshall Space Flight Center’s YouTube channel and NASA Prize’s Facebook page.
As a NASA Centennial Challenge, the Deep Space Food Challenge is a coordinated effort between NASA and CSA for the benefit of all. Subject matter experts at NASA’s Johnson Space Center and NASA’s Kennedy Space Center support the competition. NASA’s Centennial Challenges are part of the Prizes, Challenges, and Crowdsourcing program within NASA’s Space Technology Mission Directorate and managed at Marshall. The Methuselah Foundation, in partnership with NASA, oversees the competitors.
For more information about the symposium, see the symposium website. Learn more about the Deep Space Food Challenge.
Artemis Emergency Egress System Emphasizes Crew Safety
Since NASA began sending astronauts to space, the agency has relied on emergency systems for personnel to safely leave the launch pad and escape the hazard in the unlikely event of an emergency during the launch countdown.
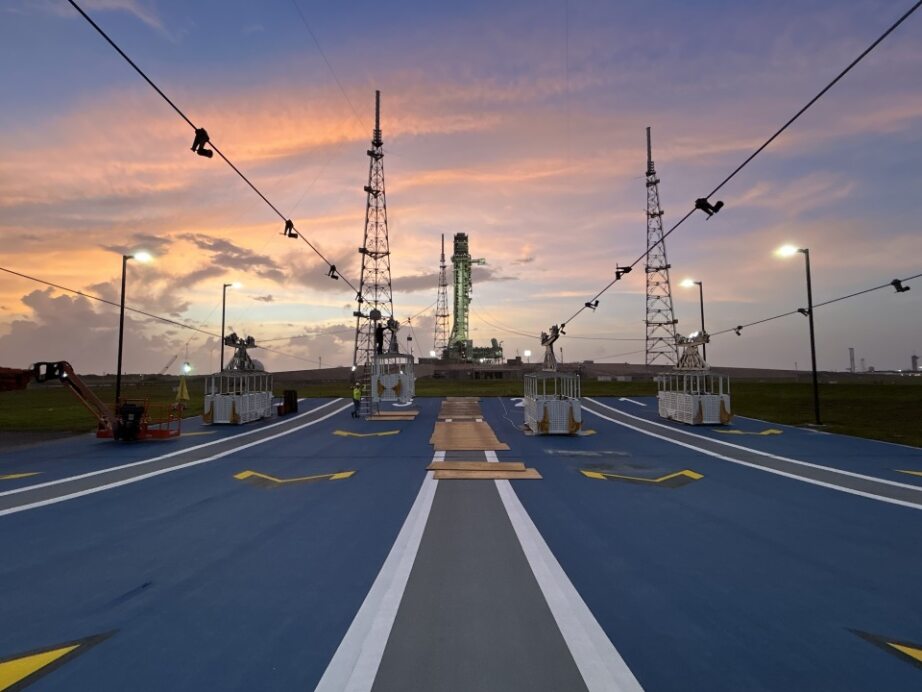
During the Mercury and Gemini programs, NASA used launch escape systems on spacecraft for the crew to safely evacuate if needed. Though these systems are still in use for spacecraft today, the emergency routes on the ground were updated starting with the Apollo missions to account for not only the crew, but all remaining personnel at the launch pad.
During Apollo, personnel relied on a ground-based emergency egress system – or emergency exit route – to allow for a quick and safe departure. Though the system has varied over time and different launch pads use different escape systems, the overall goal has stayed the same – quickly leave the launch pad and head to safety.
Beginning with Artemis II, the Exploration Ground Systems (EGS) Program at Kennedy Space Center, will use a track cable which connects the mobile launcher to the perimeter area of the launch pad where four baskets, similar to gondolas at ski lifts, can ride down. Once down at the ground level, armored emergency response vehicles are stationed to take personnel safely away from the launch pad to one of the triage site locations at Kennedy.
“We have four baskets that sit on the side of the mobile launcher tower at the same level as the crew access arm, the location where the crew enters the spacecraft,” said Amanda Arrieta, mobile launcher 1 senior element engineer for NASA’s EGS Program. “The intention is to provide another means of egress for the crew and the closeout crew in the event of an emergency. Each of these baskets will go down a wire. It’s a wire rope system that connects to the pad terminus, an area near the pad perimeter where the baskets will land after leaving the mobile launcher tower.”
The Artemis system works like this: personnel will exit the Orion spacecraft or the white room (depending where teams are at the time of the emergency) inside the crew access arm of the mobile launcher. Located on the 274-foot-level, teams are approximately 375 feet above the ground. From there, they will head down the 1,335-foot-long cables inside the emergency egress baskets to the launch pad perimeter, or the pad terminus area. Each basket, which is similar in size to a small SUV, is designed to carry up to five people or a maximum weight of 1,500 pounds.
Once teams have left the terminus area and arrive at the triage site location, emergency response crews are there to evaluate and take care of any personnel.
“When we send our crews to the pad during launch, their safety is always at the forefront of our minds. While it is very unlikely that we will need the emergency egress and pad abort systems, they are built and tested to ensure that if we do need them then they are ready to go,” said Charlie Blackwell-Thompson, Artemis launch director. “Our upcoming integrated ground systems training is about demonstrating the capability of the entire emergency egress response from the time an emergency condition is declared until we have the crews, both flight and ground, safely accounted for outside the hazardous area.”
For the agency’s Commercial Crew Program, SpaceX uses a slidewire cable with baskets that ride down the cable at the Launch Complex 39A pad. At Space Launch Complex 40, meanwhile, the team uses a deployable chute for its emergency egress system. Boeing and United Launch Alliance also use a slidewire, but instead of baskets, the team deploys seats that ride down the slide wires, similar to riding down a zip line, at Space Launch Complex 41 at Cape Canaveral Space Force Station.
Artemis II will be NASA’s first mission with crew aboard the SLS (Space Launch System) rocket and Orion spacecraft and will also introduce several new ground systems for the first time – including the emergency egress system. Though no NASA mission to date has needed to use its ground-based emergency egress system during launch countdown, those safety measures are still in place and maintained as a top priority for the agency.
NASA Sends More Science to Space, More Strides for Future Exploration
New experiments aboard NASA’s Northrop Grumman 21st cargo resupply mission aim to pioneer scientific discoveries in microgravity on the International Space Station.
Northrop Grumman’s Cygnus spacecraft, filled with nearly 8,500 pounds of supplies, launched Aug. 4 atop a SpaceX Falcon 9 rocket from Space Launch Complex 40 at Cape Canaveral Space Force Station. Biological and physical investigations aboard the spacecraft included experiments studying the impacts of microgravity on plants (grass), how packed bed reactors could improve water purification both in space and on Earth, and observations on new rounds of samples that will allow scientists to learn more about the characteristics of different materials as they change phases on the tiniest scales.
Grass Growth & Bio-Regenerative Support
The cultivation of plants is crucial for developing bio-regenerative life support systems in space. However, growing them in microgravity affects photosynthesis, the process by which plants generate oxygen and convert carbon dioxide into food for astronauts. The C4 Photosynthesis in Space Advanced Plant Experiment-09 investigation will study how two grasses (Brachypodium distachyon and Setaria viridis), with different approaches to photosynthesis, respond to microgravity and high carbon dioxide levels during the spaceflight. The insights gained from this research will pave the way for more effective integration of plants on Earth and in future space habitats. This experiment was originally scheduled to be aboard NASA’s SpaceX 30th cargo resupply mission but was moved to the NG-21 launch.
Water Purification & Gravity
The Packed Bed Reactor Experiment – Water Recovery Series aboard NG-21 will be operated on the space station and will study the hydrodynamics (pressure drop, flow regimes, and flow instability) of two-phase flow (nitrogen gas-water mixture) in microgravity in various types of filters and openings. These samples are important for fluid systems used in life support and water purification and recovery processes. Outcomes of this research will be used to develop design tools and correlations for pressure drop prediction across the various prototypes used in lunar and Martian missions and beyond.
Removing Impurities in Melted Materials
The Electrostatic Levitation Furnace–4 experiment led by JAXA (Japan Aerospace Exploration Agency), one of NASA’s space station international partners, includes 20 new test samples. Its goal is to continue establishing guidelines for measuring different thermophysical properties of various samples at temperatures greater than 2,000 degrees Celsius.
Transforming raw materials from a liquid to solid form requires the use of a container, known as a crucible, which is used to both heat and hold the substance as it cools down and hardens. During this process, a chemical reaction occurs between the substance and the crucible, and impurities are released and absorbed in the plasma. The Electrostatic Levitation Furnace is the hardware that allows scientists to remove this contaminating part of the process by creating space between the liquid and container – levitating the sample while heated.
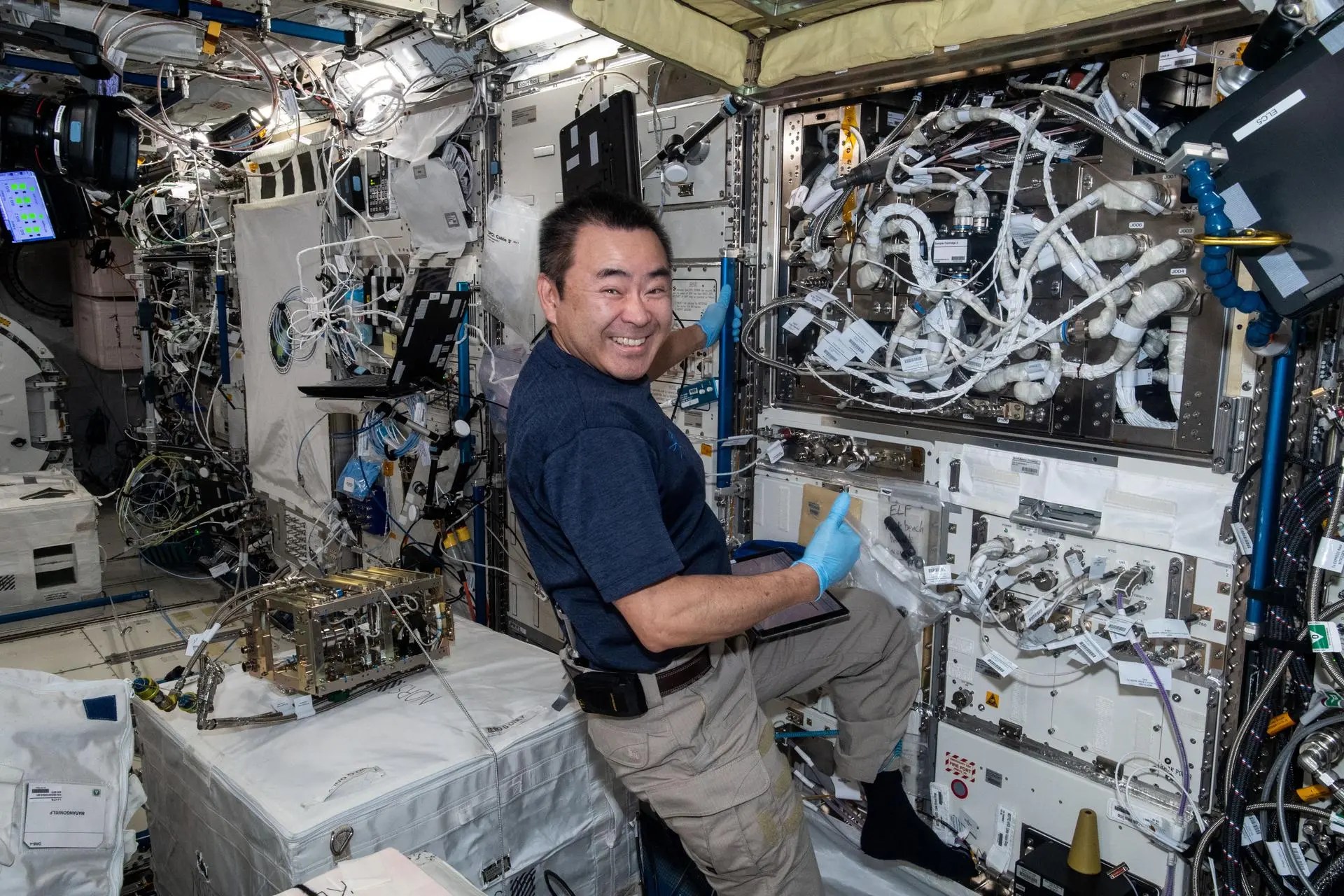
More Materials Science: Getting to the Core
The Electromagnetic Levitator, an ESA (European Space Agency) levitation facility, which is celebrating a decade aboard the International Space Station, enables scientists to conduct materials research on at least two elements, known as alloys, in a microgravity environment. By studying the core of the physics taking place, researchers can perform experiments to better understand the steps leading up to solidifying and changing phases. This knowledge could contribute to advancements in the manufacturing industry by providing scientists with more information to develop the latest and more reliable materials for activities like 3D printing.
NASA’s Biological and Physical Sciences Division pioneers scientific discovery and enables exploration by using space environments to conduct investigations not possible on Earth. Studying biological and physical phenomenon under extreme conditions allows researchers to advance the fundamental scientific knowledge required to go farther and stay longer in space, while also benefitting life on Earth.
The Huntsville Operations Support Center (HOSC) at NASA’s Marshall Space Flight Center provides engineering and mission operations support for the space station, the Commercial Crew Program, and Artemis missions, as well as science and technology demonstration missions. The Payload Operations Integration Center within HOSC operates, plans, and coordinates the science experiments onboard the space station 365 days a year, 24 hours a day.
Share
Details
Related Terms
What's Your Reaction?
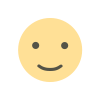
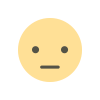
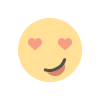
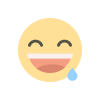
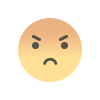
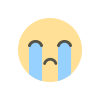
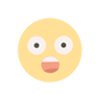